The Dairy Dilemma: Can the detectives ensure a healthy ROI from NIR?
Chapter 51
📂 Case overview: A dairy producer who wants to modernize their processing facility has been advised to embark on a costly upgrade. They are looking into installing NIR at critical points in their manufacturing process, but the boss fears that the costs cannot be justified. Can the detectives’ experience help the client with their dairy dilemma and make an informed decision to ensure the company’s profitability? Read on to find out.
After a relaxing break and a not-so-relaxing weekend helping Shallot Holmes’ friend Sue update her lab with the latest cloud-connected instruments, the detectives are back in the office awaiting a new case to sink their teeth into. Holmes works through the backlog of emails while the rest of the detectives drink coffee. “Could you pass the milk?” Miss Mapple asks Cornlumbo, and as he turns to grab the milk, Holmes yells in delight at an exciting new case for the detectives. Startled by the noise, Cornlumbo knocks down the milk and spills it all over Eggcule Poirot. “A Dairy Dilemma,” says Holmes. “That’s putting it lightly,” says Eggcule, now covered in milk. “Oh dear,” says Holmes as he turns towards Eggcule noticing what has happened. “I wasn’t even referring to the spilled milk; we have a new client at a dairy processing facility that needs our help,” Holmes explains.
As Eggcule gets cleaned up, Holmes explains the case details to the detectives. A new client has heard about the detective’s experience with NIR and is seeking advice about a potential investment. Nancy Beef instantly starts rubbing her hands, as she has much experience in this area. She reminds the detectives of her case that got the detectives their first-ever returning client. She saved a sugar cane producer €180,000 a year, and the client was so happy that they asked for the detective’s help with their bioethanol production. By optimizing its workflow, Nancy Beef saved the company a further €468,000 annually. Eggcule remembered another case where he improved the oil extraction rate of a palm oil mill which also increased its profitability. “Well then, it looks like the client has come to the right place,” declares Holmes as the detectives gather their things and set about solving the dairy dilemma.
‘A new client has heard about the detective’s experience with NIR and is seeking advice about a potential investment.’
On route, Holmes gets the detectives to consider what might influence the case. “One factor to consider is how they currently perform their analysis,” says Nancy Beef. She explains that processing facilities either conduct analysis in-house or outsource the work to a 3rd party. “Will this affect whether purchasing NIR equipment is profitable?” asks Cornlumbo. Nancy tells Cornlumbo that NIR can save processing facilities money either way. “If processing facilities are equipped to do in-house analysis with typical wet chemistry methods, then it is likely that they are spending money on solvents and other consumables that are not required when performing NIR analysis. Such facilities save money on solvents, waste disposal, and glassware that needs regular cleaning. NIR is also much faster, allowing lab technicians to focus on other tasks,” she says. “But what if they outsource their analysis? Then surely they are not making all these savings,” declares Cornlumbo. “Not necessarily. If you are only testing a few samples a month, then perhaps the purchase would not be justified; however, there are a number of factors to consider. Sending samples for analysis by a 3rd party is a slow process. Often you won’t receive the results until the next day, which creates a bottleneck in your production workflow. Also, infrequent testing may lead to quality issues due to inconsistent or mislabeled raw goods – these can negatively affect your brand and the success of your business,” says Nancy Beef, who explains that to understand the potential return on investment for a facility, you must first know the specifics of their business, which she is very keen to do!
‘If processing facilities are equipped to do in-house analysis with typical wet chemistry methods, then it is likely that they are spending money on solvents and other consumables that are not required when performing NIR analysis.’
On arriving at the facility, the detectives are greeted by a keen lab technician and the factory owner, who looks far more anxious. “Thank you for coming to see us, detectives; I do hope you can help; my fellow lab workers and I are keen to implement NIR as we know you can obtain results in seconds rather than hours,” says the lab technician. The factory owner quickly interrupted, “This is all well and good, but not if the equipment cost causes us to go bust. I understand that you technicians want the best equipment, but I need to consider the company’s profitability,” he says frustratedly. Nancy Beef steps in and explains that the only way to find out is by analyzing the potential return on investment. She gets to work firing questions at the lab technician and the owner about what they produce and how. The owner tells the detectives they produce dairy powders, butter, whey, and consumer milk, and the lab technician explains that they produce the powders by spray drying and perform all their analysis in-house, but it is very time-consuming.
Nancy gets to work assessing the facility, asking questions, and taking notes. She looks at the raw material intake, the separation & segregation area, the process control, and the final products. After meticulously analyzing each step of their process, she starts tapping away on her laptop before presenting her findings. “According to my analysis, I believe you can make a very healthy return on investment if you implement NIR at critical stages of your production. By installing NIR, where you accept your raw materials, you can assess the quality of each truckload. From what I can gather, in your industry, the quality of raw materials is influenced by the seasons and from farm to farm. The instant assessment offered by NIR ensures you maintain standards and don’t overpay for out-of-spec goods. Also, the area where you separate and segregate the incoming goods could be optimized to allow increased product consistency ensuring seamless processing from the start. In fact, throughout your process, optimizations can be made. Increasing the frequency of results eliminates numerous quality control issues, ensures product consistency, and enables process optimization. Regular information about critical parameters saves many of the reworking processes you currently undertake. Lastly, verification of your final product quality before delivery is essential as it saves costly recalls and potentially your reputation. Rather than testing a representative sample as you currently do, you can ensure the quality of all your produce,” explains Nancy, to the delight of the lab technician. The owner is looking more convinced but still slightly apprehensive. “I thought you might prefer a more concrete example specifically related to your business,” says Nancy, and she hands the owner a graph
‘Increasing the frequency of results eliminates numerous quality control issues, ensures product consistency, and enables process optimization.’
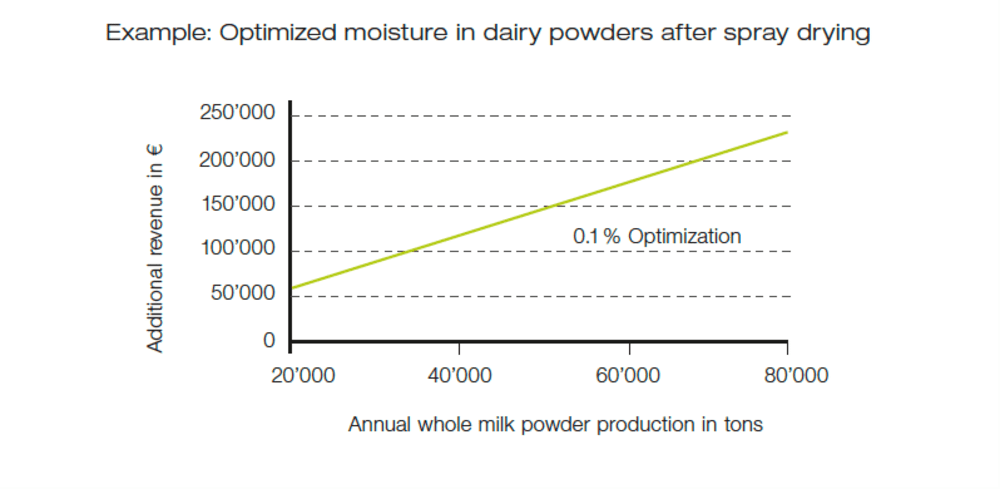
“Your average milk powder has a moisture content of 3 % and a market price of €3 per kg, and you produce 54 tons daily. Process optimization that results in a 0.1 % improvement would mean 1 kg more moisture per ton of whole milk powder, creating €162 per day, or €58,000 annually,” says Nancy. The owner is now looking far less distressed. “Similar optimization of your butter churning process could make you up to €65,000 annually, says Nancy handing the owner another graph.
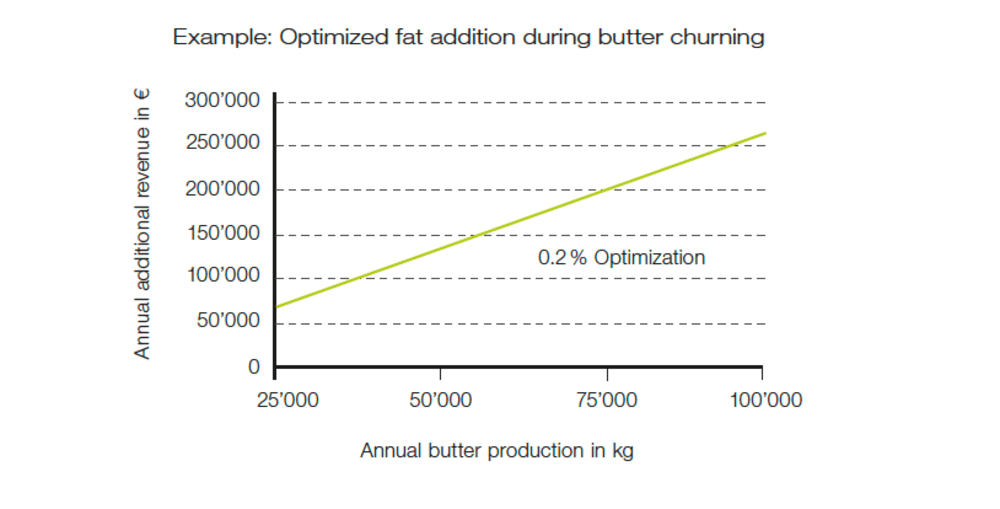
‘Process optimization that results in a 0.1 % improvement would mean 1 kg more moisture per ton of whole milk powder, creating €162 per day, or €58,000 annually.’
“And those are just the savings you make through process optimization; there are also the time and cost savings I have already mentioned, and the environmental benefits of a huge reduction in the solvents used by traditional wet chemistry methods,” concludes Nancy. “Well, how can I refuse if you put it like that? And think of all the time I will save not having to listen to my lab technicians pleading and begging me to make this upgrade,” says the owner with a big grin on his face. The lab technicians and the detectives laugh heartily and congratulate Nancy Beef on a job well done.