How the sugar cane producer saved another €468,000 during bioethanol production
Chapter 38
📂 Case overview: The food detectives were happy to help a sugar cane producer already save €180,000 during the four steps of raw cane sugar production. They are even more happy when he returns for advice on how to optimize his bioethanol production processes. Can you believe that they manage to save him another half a million/year? How Nancy Beef manages this fantastic feat using NIR technology is described in the post below.
Shallot Holmes has just received an exciting phone call. One of their clients is so pleased with their work, he has hired the agency for further consulting. The detectives are ecstatic, their first return customer!
The client, a sugar cane producer, has already seen huge savings from introducing NIR technology to monitor sugar cane production. He is happy to invest into branching out further and entering the field of bioethanol production. Nancy Beef, as his main point of contact, is proud to land this case as well. She begins to prepare for the case by reading a quick guide on how to use NIR to boost profitability.
She then flies in to visit her customer and to see how the addition of bioethanol production has affected his workflow:
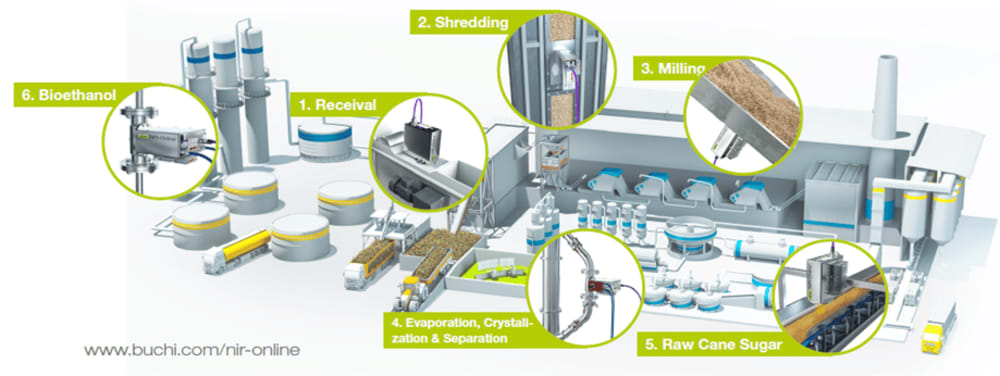
The client shows her the addition of the equipment needed for bioethanol production and refreshes Nancy Beef’s memory on how the process works. He outlines the steps needed to obtain sugarcane bioethanol fuel:
- Fermentation of cane juice or molasses
- Distillation
- Rectification
- Dehydration
Nancy Beef observes carefully and notes that continuous knowledge of feed-stock composition is pivotal to boosting the fermentation efficiency and therefore final bioethanol yield. Similarly, the client should monitor the ethanol content during the distillation step. This would enable the operators to make any necessary process adjustments in real-time and maximize final bioethanol yield. Not to be forgotten is the quality of the final product before delivery. Parameters should also be analyzed to ensure the bioethanol is of top-notch grade prior to storage and shipment.
She suggests that the parameters the bioethanol producer needs to analyze during distillation, rectification, dehydration and monitoring of final product quality include:
- Brix
- Moisture
- Ethanol
- Density
- Flash point
- Cloud point
Nancy Beef points out the challenges that could arise if the bioethanol production step goes unmonitored. The client would have no representative of the average quality of feedstock and no control over the production steps. The operators would only receive late notice if re-work needs to be performed, leading to more complex, expensive, and time-consuming re-work procedures. The process and products would be subjected to quality fluctuations, and it would be extremely difficult to achieve any traceability in the bioethanol production process.
If instead, the client chooses to implement NIR technology for quality monitoring during bioethanol production, things would look quite different. He would receive a true average value of the most relevant parameters in sugarcane juice and molasses. With an NIR system, he could exercise real-time control of the fermentation, distillation, and dehydration step. As a result, he would improve ethanol yield and product quality with full traceability and documentation of his bioethanol production workflow.
The client does not need much more convincing. He agrees to set up another NIR system directly online at his plant. He promises to report on the results a year later.
The sugar cane producer stays true to his promise. He calls Nancy Beef in a year’s time, beaming with positive results thanks to his investment in NIR instruments. He shares the following ROI calculation:
His daily sugarcane crushing capacity for bioethanol production is 4000 tons at a total revenue of €128,000, considering that 1 ton of sugar cane produces around 80 liters of bioethanol at an average price of €0.45/liter. An increase in ethanol yield by only 1% results in 3200 liters of additional bioethanol per day. This corresponds to an annual production increase of 1,168,000 liters and additional revenue of €467,200.
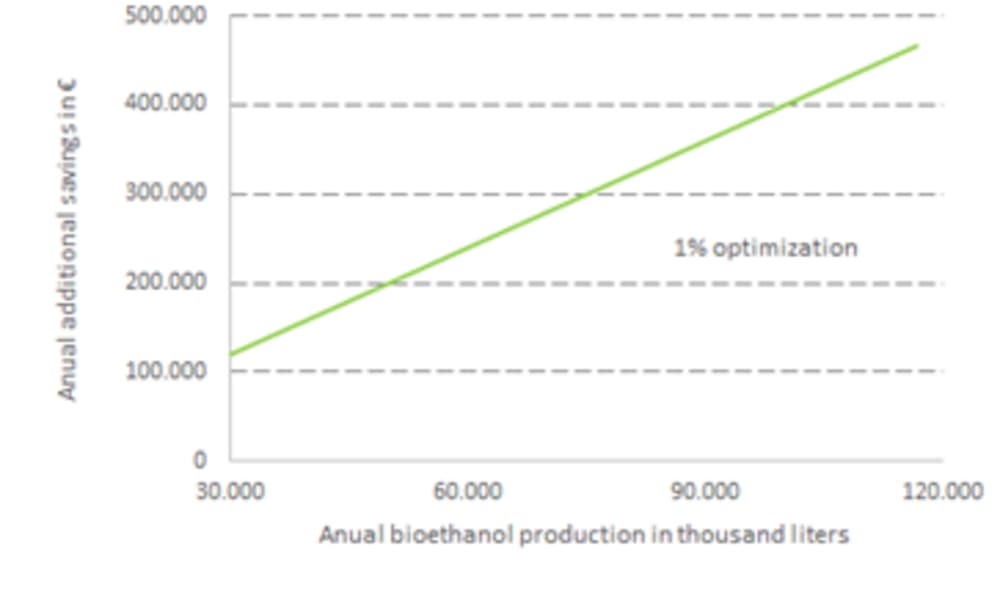
The food detectives celebrate this fantastic result! They did not just have their first return client, they now have their very first very satisfied return client!